

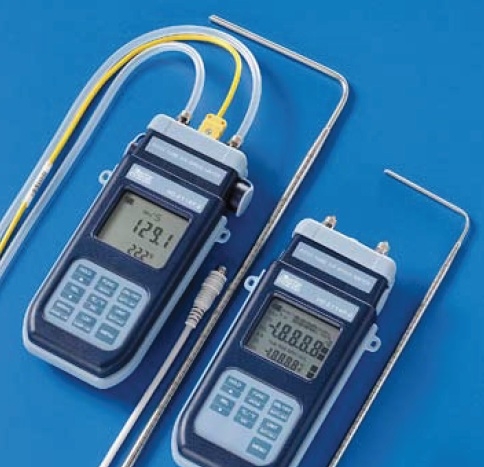
To measure impact pressure, most pitot tubes use a small, sometimes L-shaped tube, with the opening directly facing the oncoming flowstream. The total impact pressure (P T) is the sum of the static and kinetic pressures and is detected as the flowing stream impacts on the pitot opening. It is measured at right angles to the flow direction, preferably in a low turbulence location (Figure 2-9). The static pressure is the operating pressure in the pipe, duct, or the environment, upstream to the pitot tube. Basically a differential pressure (d/p) flowmeter, a pitot tube measures two pressures: the static and the total impact pressure. Pitot tubes were invented by Henri Pitot in 1732 to measure the flowing liquid or air velocity. An advantage of the slender pitot probe is that it can be inserted into existing and pressurized pipelines (called hot-tapping) without requiring a shutdown.
#USING A PITOT TUBE TO MEASURE AIR VELOCITY FULL#
The main difference is that, while an orifice measures the full flowstream, the pitot tube detects the flow velocity at only one point in the flowstream. Its flow rangeability of 3:1 (some operate at 4:1) is also similar to the capability of the orifice plate. Accuracy ranges from 0.5% to 5% FS, which is comparable to that of an orifice. The pitot tube is an inexpensive alternative to an orifice plate. While accuracy and rangeability are relatively low, pitot tubes are simple, reliable, inexpensive, and suited for a variety of environmental conditions, including extremely high temperatures and a wide range of pressures.
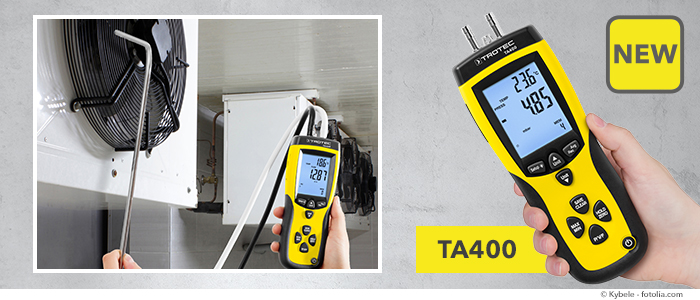
In industrial applications, pitot tubes are used to measure air flow in pipes, ducts, and stacks, and liquid flow in pipes, weirs, and open channels. Although the pitot tube is one of the simplest flow sensors, it is used in a wide range of flow measurement applications such as air speed in racing cars and Air Force fighter jets.
